Clinker Grinding Quartz
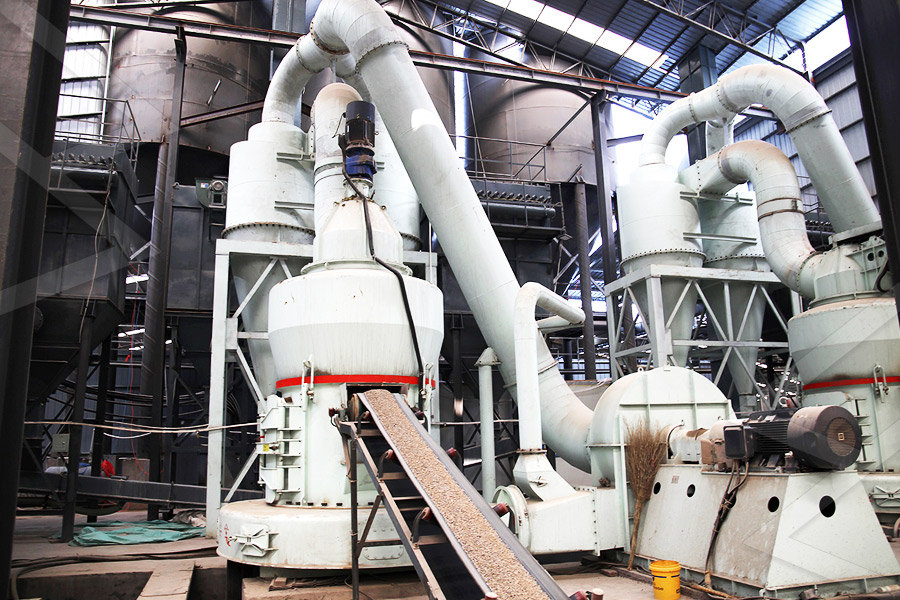
Effects of grinding aids on the grinding kinetics and surface
2023年10月1日 Deniz studied investigates the effect of milling speed on the kinetic breakage parameters for clinker and limestone during grinding The results showed that increasing the 2024年7月21日 This study investigates the influence of the quartz content and particle size in siliceous limestone on the calcination process and the resultant quality of cement clinker Two different siliceous limestones were grinded to Effects of Fineness and Morphology of Quartz in 2024年7月31日 Quadratic regression models exhibited strong predictive capabilities for energy consumption in grinding Ultimately, the optimal grinding performance was achieved with Bondtype ball distribution No 6, considering Effect of Grinding Conditions on Clinker 1979年3月1日 Four commercial Portland clinker samples with different chemical compositions and grindability indices were examined It was found that clinker with low percentage of Al 2 O Effect of clinker composition on grindability ScienceDirect2022年8月25日 High quartz content in clay substantially impacts the grinding of raw mix, quality of clinker and final cement produced The presence of quartz requires very fine grinding and a Effect of Quartz in Clay on Grindability of Raw Mixes for The grinding of clinker depends on the chemical composition and mineralogical properties; high content of alite and low content of belite and interstitial phases (aluminate and ferrite) is easier (PDF) Study Of The Clinker Characteristics And Grindability
.jpg)
Influence of Clinker Microstructure on Grinding Efficiency in
2020年7月31日 Numerous experiments on the study of the kinetics of dispersion of mineral rocks show that grinding in laboratory mills can predict the evolution of particle sizes 2023年10月23日 Grinding aids can improve production and fineness and decrease energy consumption by reducing the agglomeration of particles and protecting the balls and liners in the mill In this study we(PDF) A study of different grinding aids for low 2020年7月31日 The action mechanism of surfactants and increasing the efficiency of grinding mineral powders have been repeatedly studied and discussed In some works, the action mechanism of surfactants is explained from the point of view of the Rebinder theory (Rebinder effect) [1, 2], in other works, the effect of surfactants is reduced only to a decrease in the Influence of Clinker Microstructure on Grinding Efficiency in 2021年1月10日 Grinding aids (GAs) are incorporated during comminution of clinker to reduce electrostatic forces and minimize agglomeration of clinker and SCM grains [15]Their chemical compositions include alkanolamines such as triethanolamine (TEA), triisopropanolamine (TIPA) and diethylisopropanolamine (DEIPA), as well as glycols such as propylene glycol (PG), Assessing the effect of alkanolamine grinding aids in 2009年5月1日 The evaluation of the grinding aids (GA) was carried out by interground 0015% of each grinding aid with gypsum and a Portland cement clinker (95% clinker, 5% gypsum), in a 1 kg laboratory rotating ball mill, using steel balls as grinding medium, to a Blaine surface area of about 4000 cm 2 /g (according to the Blaine air permeability method) [14]Characterization of various cement grinding aids and their 2020年4月14日 Grinding aids (GAs) are incorporated during comminution of clinker to reduce electrostatic forces and minimize agglomeration of clinker and SCM grains Such additions are commonly used to increase cement fineness and compressive strength for given specific energy consumption (Ec) of the grinding mill [ 1 , 2 , 3 ]Improving the Behaviour of Calcined Clay as Supplementary
.jpg)
(PDF) Study Of The Clinker Characteristics And Grindability
The grinding of clinker depends on the chemical composition and mineralogical properties; high content of alite and low content of belite and interstitial phases (aluminate and ferrite) is easier to grind than the clinker rich in belite and interstitial phases densely packed crystals due to coarse quartz in feed causing hard clinker and 2020年9月20日 Grinding aid additives are established in various industrial dry fine grinding processes, primarily to achieve either a) an increase of the production capacity, b) a decrease of the specific energy consumption or c) finer particles or a better product performance However, even though numerous related scientific papers have already been published and a variety of Grinding aids for dry fine grinding processes ScienceDirect2013年4月25日 The cement manufacturing stages of raw grinding, kiln burning and clinker cooling Key factors like raw mix characteristics, burning process, and clinker/cement composition influence the quality 3 Different cement types produced for various applications and their requirements in terms of clinker quality, additive quality and physical Cement raw mix characteristics PPT SlideShareClinker is the primary material of cement, and it is called as semifinished product Clinker is a granulated material made of raw meal powder obtained by grinding limestone and clay together by sintering the raw meal in a rotary furnace at 1400°C1500°C degrees Produced clinker’s mineralogical structure effects clinker’s grinding energyWhat is Clinker? The Relationship Between Clinker Phases and Grinding 2020年9月20日 Scheibe et al [25] carried out an extensive investigation of various grinding aids on the batchwise grinding of cement clinker, quartz and limestone in the 1970s They found that the impacts of the applied chemical on parameters like the product fineness or the material adhesions inside the mill depend on a complex relation between the ground Grinding aids for dry fine grinding processes ScienceDirect1983年1月1日 The range of clinker composition may be fairly wide if the amount of liquid phase increases slowly [55] A clinker with about 25% liquid phase from a raw mix is generally considered an ideal raw mix for kiln lining, fuel saving, rapid C3S formation through dissolution of C2S and CaOr and economical clinker grindingBurnability and Clinkerization of Cement Raw Mixes
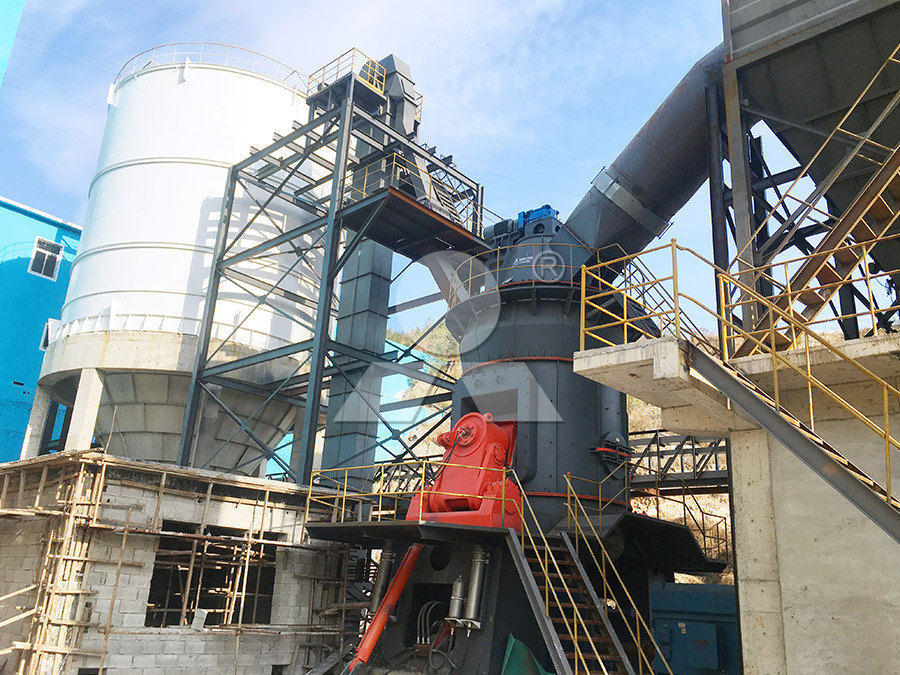
Influence of Clinker Microstructure on Grinding Efficiency in
2020年7月1日 Grinding processes in cement production technology are quite energyintensive The mechanism of action of surfactants on the course of the clinker grinding process has not been fully studied2022年1月1日 The aim of this work is to study changes in the properties of aqueous corundum suspensions during ultrafine grinding with and without the addition of an activator Corundum suspensions were prepared in distilled water in a ratio of 1:5 with and without the addition of triethanolamine (TEA) and ground using a planetary ball mill Particlesize distribution, ζ Ultrafine wet grinding of corundum in the presence of triethanolamine2019年6月22日 Grinding aids (GAs) are incorporated during comminution of clinker to reduce electrostatic forces and minimize agglomeration of clinker and SCM grains Such additions are commonly used to increase cement fineness and compressive strength for given specific energy consumption (Ec) of the grinding mill [ 1 , 2 , 3 ]Processing of Calcined Clays for Applications in Springer2024年7月21日 With the increasing depletion of highquality raw materials, siliceous limestone, sandstone and other hardtoburn raw materials containing crystalline SiO2 are gradually being used to produce clinker This study investigates the influence of the quartz content and particle size in siliceous limestone on the calcination process and the resultant quality of cement Effects of Fineness and Morphology of Quartz in Siliceous 2023年10月1日 Deniz studied investigates the effect of milling speed on the kinetic breakage parameters for clinker and limestone during grinding On this basis, the effects of grinding aids on the kinetic parameters for quartz grinding with scanning electron microscopy, specific surface area and contact angle determinations to probe the surface Effects of grinding aids on the grinding kinetics and surface Portland cement is a fine powder produced by grinding Portland cement clinker (more than 90%), a limited amount of gypsum (calcium sulphate dehydrate – CaSO42H2O, which controls the set time) and other minor constituents which can be used to vary the properties of the final cement The standard Portland cement is often referred to as Portland Cement Clinker an overview ScienceDirect Topics

Investigating multicomponent breakage in cement grinding
2015年6月1日 A sampling campaign was performed around the cement grinding circuit, during the CEM II BM (P–W) 325R type blended cement production In accordance with EN 1971, CEM II BM (P–W) type cement is composed of 65–79% cement clinker and 21–35% pozzolan + calcareous fly ashThe term “CEM II BM” indicates Portland composite cement relatively low 1979年3月1日 It was found that clinker with low percentage of Al 2 O 3 and Fe 2 O 3 is easier to grind Clinker with higher percentage of liquid phase shows a higher work index, ie, hard to be ground No 2 GR Gouda presence of quartz which is characterized by its major peak at 3343 dspacing (2665°28), a strong peak at 182 dspacing (5035°28 Effect of clinker composition on grindability ScienceDirect2023年7月4日 The use of hightemperature Xray diffraction (HTXRD) to study the mass transfer of raw meal constituents towards forming clinker phases and the occurrence of free lime (calcium oxide), also known as burnability, was assessed A measuring strategy with temperature ranging from 1000°C to 1450°C was developed and compared with a conventional burnability Phase evolution and burnability of cement raw mealGrinding Mill Supplier, Raymond Mill, Ball Mill Manufacturers/ Suppliers Shanghai Clirik Machinery Co, Ltd Clirik Barite Limestone Kaolin Clinker Graphite Calcite Feldspar Fluorite Raymond Mill by Audited Supplier Ball Mill by Audited Supplier for Ore Limestone Quartz Graphite Calcite Limestone Powder Production Line FOB Price: US Grinding Mill Manufacturer, Raymond Mill, Ball Mill Supplier2014年6月1日 Grinding aids are materials that are added to cement mixtures to improve the characteristics of the cement or increase the efficiency of the milling systems or both in the clinker grinding (finish (PDF) Comprehensive understanding of grinding Clinker Calcium Carbonate Dolomite Barite Quartz Marble Limestone Dust Making Machine Grinding Mill No reviews yet Shanghai Clirik Machinery Co, Ltd Custom manufacturer 11 yrs CNCalcium Carbonate Grinding Solutions Efficient Durable
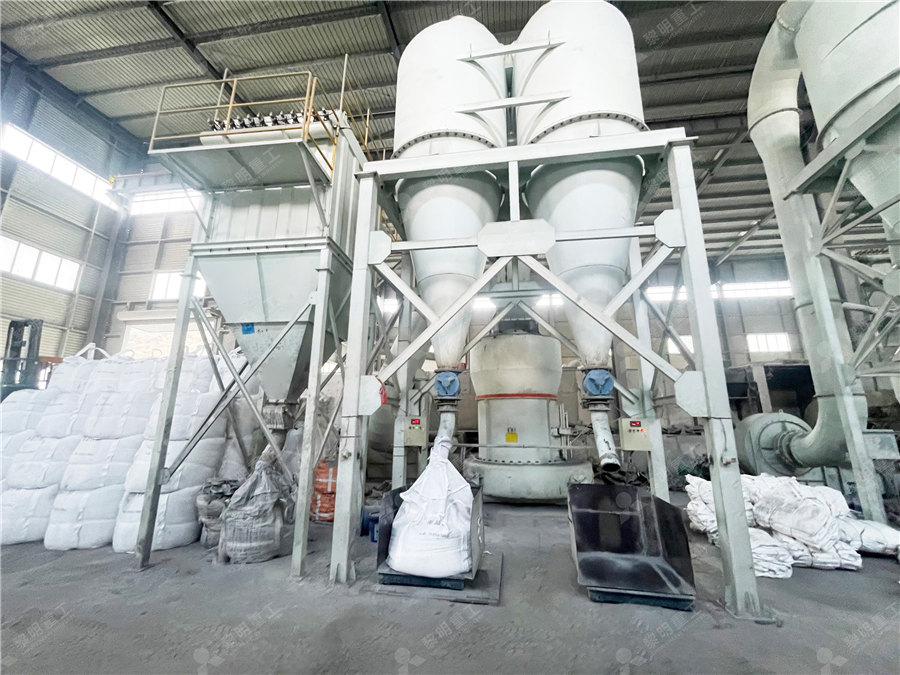
Study on the impacts of media shapes on the performance of
2020年10月1日 The cement clinker advocates firstorder breakage kinetics The shape of grinding media has a dramatic effect on the cement clinker grinding (Qian et al, 2013) Φ 2000: −475 + 118: Cylinders: 1600–4600: Average of Si = 005152 min −1: Φ 20 × 20: Ballmill Fractional ball filling: 20, 50, and 80%: Quartz: Spherical balls –Comparison between grinding of cement clinker with and without grinding aid (after Fuerstenau, 1990) Figure 1 shows the typical comparison between grinding of cement clinker with and without a grinding aid in a laboratory mill As discussed in the literature [1,2,4], there was significant effect of using grinding aid in cement grindingV RQI 6HU Design of New Slotted Structured Grinding2019年6月1日 The cement grinding mill circuit loaded approximately 95% through clinker raw materials and rest of the feeding material is performing properties enhancer [16], [17] In grinding process, the quality of cement in terms of fineness was measured by using Blaine's surface area and particle size distribution analysis [18]Investigation on grinding impact of fly ash particles and its The cement roller press is a kind of grinding equipment applied for brittle materials, such as cement clinker, granular blast furnace slag, cement raw materials (limestone, sandstone, shale, etc), gypsum, coal, quartz sand, iron ore, etcCement Roller Press Roller Press In Cement Plant Roller 2019年1月1日 Musci et al [5] have investigated the grindabilities of andesite, basalt, clinker, limestone and quartz Referring back and forth to the study of Mucsi et al [5], although it has not been VOLUME BASED CLOSEDCYCLE HARDGROVE GRINDABILITY METHODWith the increasing depletion of highquality raw materials, siliceous limestone, sandstone and other hardtoburn raw materials containing crystalline SiO 2 are gradually being used to produce clinker This study investigates the influence of the quartz content and Effects of Fineness and Morphology of Quartz in Siliceous
.jpg)
Welcomed Warmly Limestone Granite Quartz Basalt Grinding
2025年1月26日 Welcomed Warmly Limestone Granite Quartz Basalt Grinding Equipment, Find Details and Price about Clinker Grinding Plant Cement Making Machine from Welcomed Warmly Limestone Granite Quartz Basalt Grinding Equipment HENAN TURUI MACHINERY CO, LTD2015年8月29日 The clinker grinding is responsible for around 40% of the total energy usage during cement production [21] Therefore intergrinding is a potential way of saving considerable amount of energy since some mineral admixtures have a clear positive influence on the grindability of clinker 5SINTEF REPORT2020年7月31日 The action mechanism of surfactants and increasing the efficiency of grinding mineral powders have been repeatedly studied and discussed In some works, the action mechanism of surfactants is explained from the point of view of the Rebinder theory (Rebinder effect) [1, 2], in other works, the effect of surfactants is reduced only to a decrease in the Influence of Clinker Microstructure on Grinding Efficiency in 2021年1月10日 Grinding aids (GAs) are incorporated during comminution of clinker to reduce electrostatic forces and minimize agglomeration of clinker and SCM grains [15]Their chemical compositions include alkanolamines such as triethanolamine (TEA), triisopropanolamine (TIPA) and diethylisopropanolamine (DEIPA), as well as glycols such as propylene glycol (PG), Assessing the effect of alkanolamine grinding aids in 2009年5月1日 The evaluation of the grinding aids (GA) was carried out by interground 0015% of each grinding aid with gypsum and a Portland cement clinker (95% clinker, 5% gypsum), in a 1 kg laboratory rotating ball mill, using steel balls as grinding medium, to a Blaine surface area of about 4000 cm 2 /g (according to the Blaine air permeability method) [14]Characterization of various cement grinding aids and their 2020年4月14日 Grinding aids (GAs) are incorporated during comminution of clinker to reduce electrostatic forces and minimize agglomeration of clinker and SCM grains Such additions are commonly used to increase cement fineness and compressive strength for given specific energy consumption (Ec) of the grinding mill [ 1 , 2 , 3 ]Improving the Behaviour of Calcined Clay as Supplementary
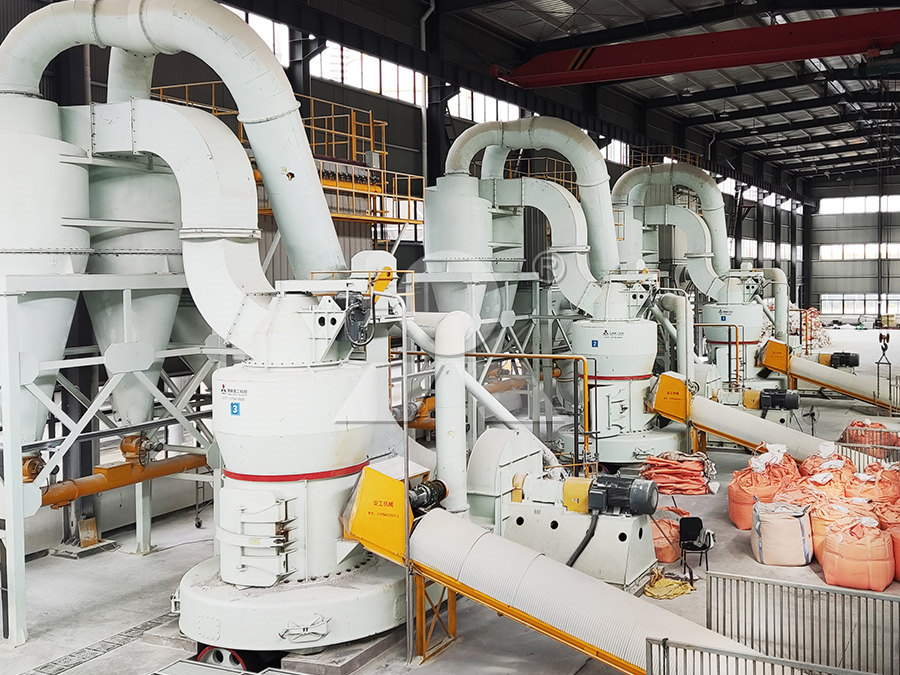
(PDF) Study Of The Clinker Characteristics And Grindability
The grinding of clinker depends on the chemical composition and mineralogical properties; high content of alite and low content of belite and interstitial phases (aluminate and ferrite) is easier to grind than the clinker rich in belite and interstitial phases densely packed crystals due to coarse quartz in feed causing hard clinker and 2020年9月20日 Grinding aid additives are established in various industrial dry fine grinding processes, primarily to achieve either a) an increase of the production capacity, b) a decrease of the specific energy consumption or c) finer particles or a better product performance However, even though numerous related scientific papers have already been published and a variety of Grinding aids for dry fine grinding processes ScienceDirect2013年4月25日 The cement manufacturing stages of raw grinding, kiln burning and clinker cooling Key factors like raw mix characteristics, burning process, and clinker/cement composition influence the quality 3 Different cement types produced for various applications and their requirements in terms of clinker quality, additive quality and physical Cement raw mix characteristics PPT SlideShareClinker is the primary material of cement, and it is called as semifinished product Clinker is a granulated material made of raw meal powder obtained by grinding limestone and clay together by sintering the raw meal in a rotary furnace at 1400°C1500°C degrees Produced clinker’s mineralogical structure effects clinker’s grinding energyWhat is Clinker? The Relationship Between Clinker Phases and Grinding 2020年9月20日 Scheibe et al [25] carried out an extensive investigation of various grinding aids on the batchwise grinding of cement clinker, quartz and limestone in the 1970s They found that the impacts of the applied chemical on parameters like the product fineness or the material adhesions inside the mill depend on a complex relation between the ground Grinding aids for dry fine grinding processes ScienceDirect1983年1月1日 The range of clinker composition may be fairly wide if the amount of liquid phase increases slowly [55] A clinker with about 25% liquid phase from a raw mix is generally considered an ideal raw mix for kiln lining, fuel saving, rapid C3S formation through dissolution of C2S and CaOr and economical clinker grindingBurnability and Clinkerization of Cement Raw Mixes